The most frequent errors made when insulating a home (part two)
In this part we continue with errors made when insulating a house with polystyrene. This time we will focus on faults while installing the insulation boards (sheets).
Incorrect displacement of sheets
Standard dimensions of polystyrene sheets are as follows: 50x100cm. They should be installed with joints displacement, just like bricks in the wall. Therefore they should be laid from the bottom, in horizontal rows of 50 cm height, by displacing the next layer of half the length of the sheet (board). It’s important to remember that the layers must interlock in the corners. This way we can prevent long horizontal joints. In addition, the boards should be firmly installed mechanically in a strip of 1m width, as stress and wind impact are the strongest there. A number of anchors is usually increased from 4 to 8 per m2. The edges themselves are reinforced with special corners and/or mesh.
The areas around openings
Unfortunately, the insulation system is a bit disrupted near window and door areas. It’s absolutely essential so that the horizontal and vertical joints of boards do not overlap with the edges of openings. In these areas we always have a concentration of stress which occurs in the wall. In the event of an incorrect system of insulation, the stress is transferred to the exterior plaster, which is subject to cracks, just along the stress lines. Corners should be cut in a shape of letter “L”, just like shown in the picture.
In addition, the insulation close to openings should not be cut into narrow strips - minimum is 25cm. It’s recommended to apply the longest board near the corner, and the narrow stripe close to the centre of the wall, as stress and wind impact is less strong there. The areas near windows and doors require more anchors, similarly to the corners. The edges themselves should be reinforced with corners and extra mesh strips. They prevent mechanical damages.
Non-filled cracks
Even if boards are correctly installed there might occur several millimetre cracks. The more uneven the substrate the bigger they are, which might result from incorrectly cut boards. This is why we should avoid using chipped or broken boards. It’s better to use them in other areas. Bigger cracks are filled with thin polystyrene strips and a low expansion foam, whereas the smaller ones with a foam only. It’s forbidden to put adhesive into cracks, as they will become thermal bridges! The adhesive can be from a reinforcing topcoat and also from the bottom layer, for installing boards to the wall. Oftentimes its excessive amount on the sides prevent the boards from matching them correctly. Therefore, any excessive amount of the adhesive should be removed with a putty knife after installing each board.
Grooved polystyrene boards are not a solution at all. They have as many opponents as supporters. Particularly on an uneven substrate the grooved edge covers partly the joint of the boards, but it does not means that the joint is tight. The grooved edge prevents application of a foam or polystyrene stripes.
All non-standard shapes might be especially troublesome, which must be covered with insulation - polygonal bays, wall corners converging at an angle different than 90°. It’s scarcely possible to cut the boards correctly in these areas and the joints must be sealed.
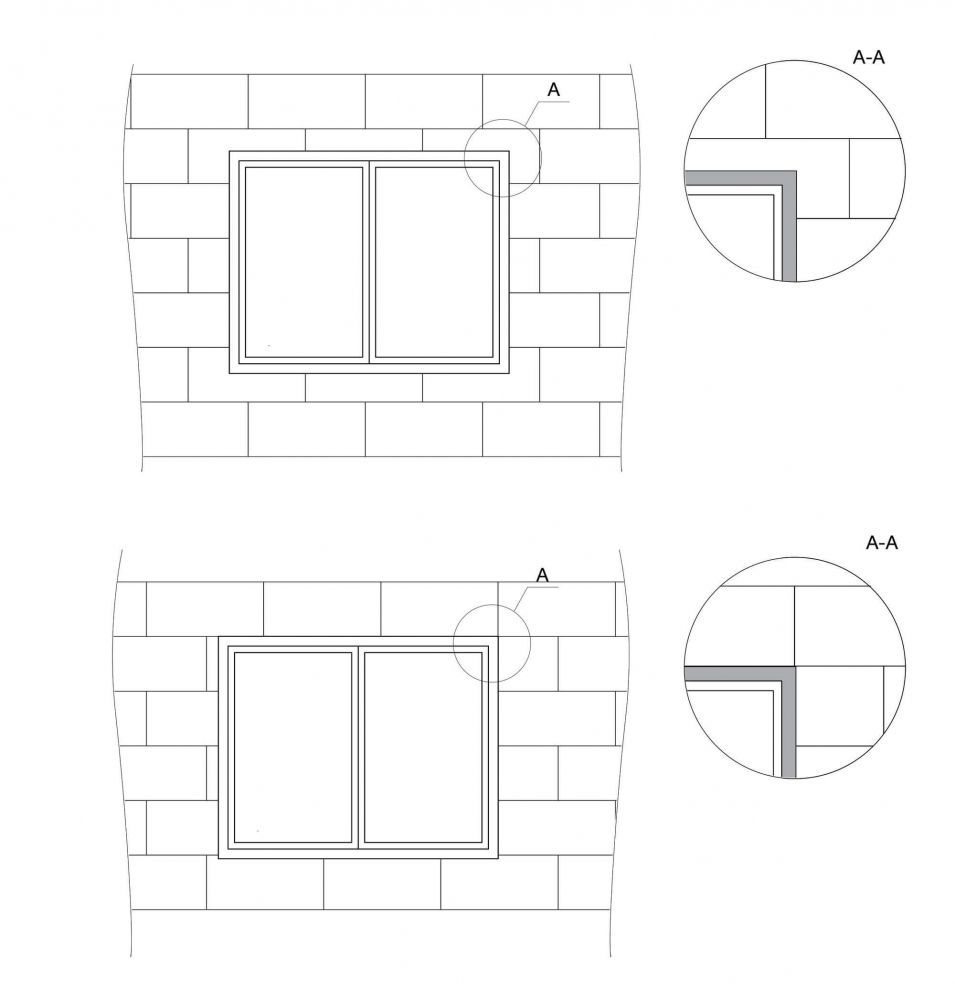
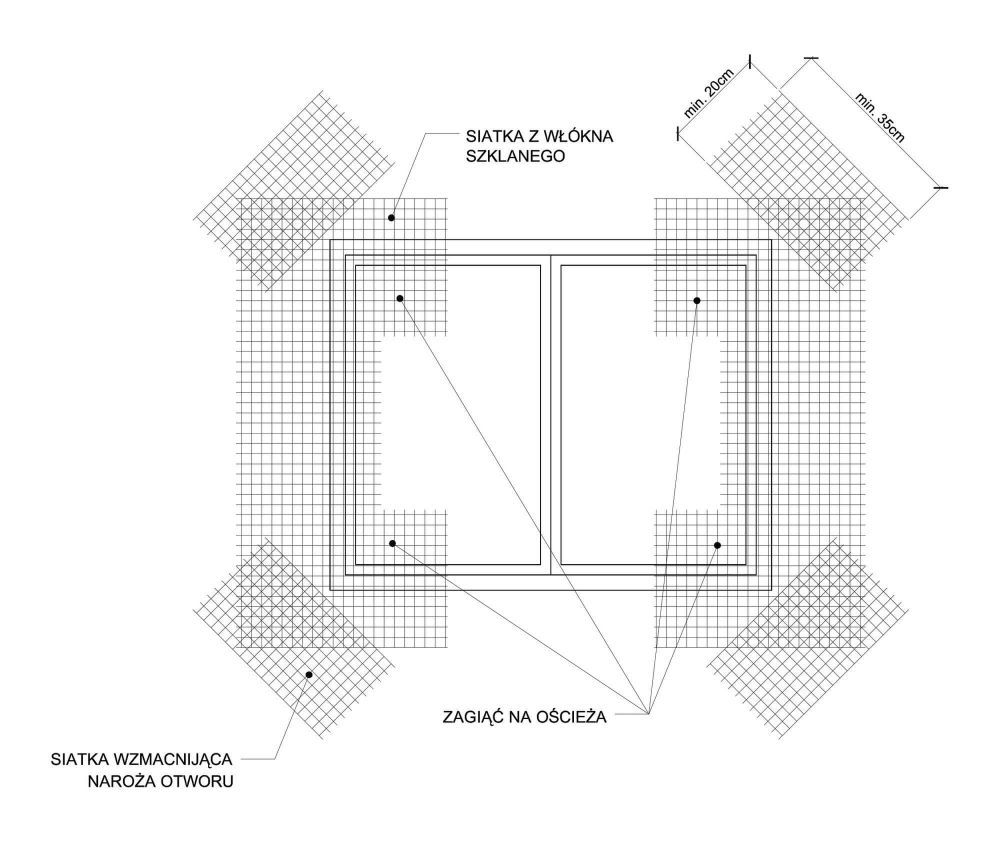
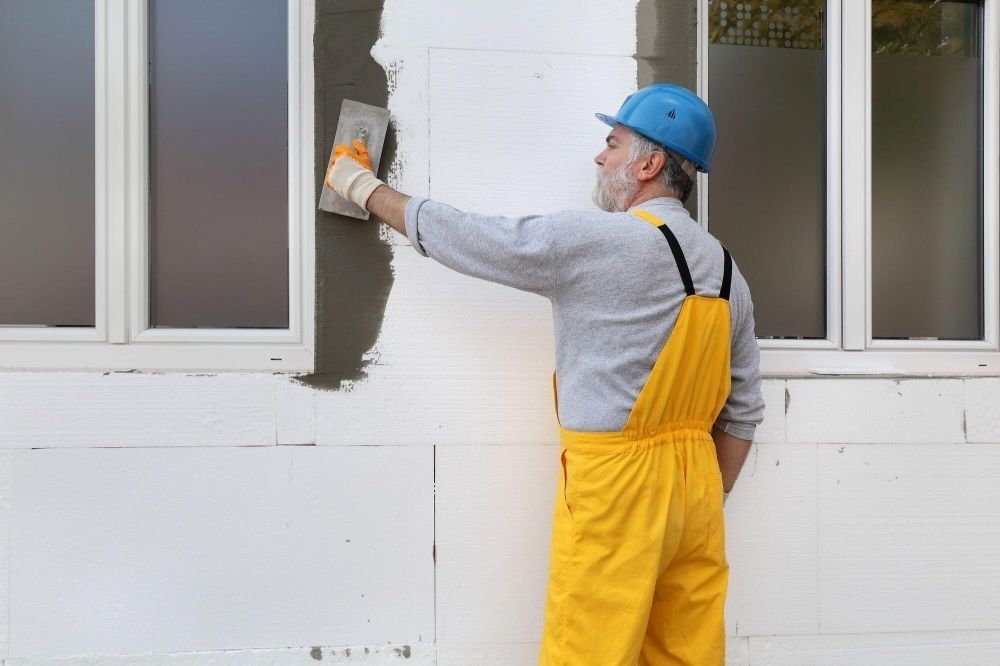